Hose failure is expensive.
A failed hose line can halt operations, resulting in lost productivity, wasted material and the potential for costly environmental fines. Not only that but failed hose assemblies can cause injury, illness or death to employees and other passersby.
Why do hoses typically fail? The top reasons why both industrial and hydraulic hose assemblies fail include:
- Improper Assembly and Fittings
- Improper Routing
- Tube Erosion
- Pressure Surges
- Fluid Incompatibility
- Inadequate Minimum Bend Radius
- Inadequate Insertion Depth
- Abrasion
- Chemical Exposure
- Dry Air
Aside from normal wear and tear, failed hose assemblies are usually due to a simple error at the time of installation. With proper operator training, you can reduce the chances of unexpected failure, saving time and money. Operators should be able to:
- Understand and identify different types of hoses (industrial and hydraulic).
- Understand the uses and limitations of each hose type.
- Choose the right hoses and fittings for each application.
- Spot signs of wear and tear and know when to replace components.
But first, operators must understand what makes a hose assembly complete.
Call customer service at 314-638-6500 OPTION 4 or toll-free 800-783-6501 and speak to a knowledgeable representative today!
What Components Make Up a Full Hose Assembly?
While there may be some similarities, hydraulic hoses have different conveyance requirements, working conditions and applications than industrial hoses and, as a result, may look and function a little different. If you use the wrong hose with the wrong application, the results can be devastating.
Let’s explore the components of each assembly.
Hydraulic Hose Assembly
- Inner Tube: The inner tube is responsible for carrying hydraulic fluid through the line. Typically, it is made of synthetic rubber or thermoplastic materials that can withstand the high-pressure commonly associated with applications requiring hydraulic fluids.
- Reinforcement Layer: The reinforcement layer provides structural integrity and strength to the hydraulic hose assembly. It is usually made of multiple layers of braided or spiral-wound steel wire or synthetic fibers such as aramid or polyester. The reinforcement layer prevents the hose from bursting under high-pressure conditions.
- Outer Cover: The outer cover protects the inner tube and reinforcement layers from environmental factors such as abrasion, chemicals and UV radiation. It is constructed from synthetic rubber or thermoplastic materials and may have additional protective layers like textile braid or wire mesh.
- Fittings: Fittings are the end connections of the hydraulic hose assembly, enabling it to be attached to other components of the hydraulic system. They provide a secure and leak-free connection. Common types of fittings include crimped fittings, reusable fittings or quick disconnect couplings.
Related: Superior’s Simple Guide to Understanding Hydraulic Hose and Fitting Assembly
Industrial Hose Assembly
- Inner Tube: Similar to hydraulic hose assemblies, industrial hose assemblies also have an inner tube that carries fluid such as water, air, chemicals and abrasive materials. The inner tube material depends on the specific application and the type of fluid being conveyed. It can be made of materials like natural or synthetic rubber, PVC, polyethylene or Teflon.
- Reinforcement Layer: The reinforcement layer in an industrial hose assembly provides strength and flexibility to the hose. It can consist of various materials such as textile fibers, wire helix or synthetic yarns. The reinforcement layer ensures the hose can withstand pressure and maintain its shape during use.
- Outer Cover: The outer cover of an industrial hose assembly serves the same purpose as in a hydraulic hose assembly, protecting the inner layers from abrasion, chemicals and other external factors. It is typically made of synthetic rubber or thermoplastic materials.
- Couplings: Industrial hose assemblies use couplings as end connections to join the hose with other equipment or systems. These couplings may include clamps, quick-connect fittings, cam and groove fittings, or specialized fittings depending on the application requirements.
Related: Hydraulic Hose Assembly Routing Guidelines to Extend Service Life
All hose assemblies are comprised of four similar elements.
- Inner Tube
- Reinforcement Layer
- Outer Cover
- End Connections (fittings and couplings)
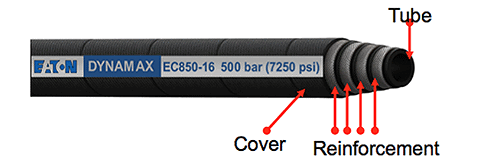
Source: Hose Assembly Tips
Additionally, there are fitting components usually made of metal such as steel, carbon steel or brass. Fittings are typically comprised of a socket and stem. A socket is the part of the fitting that goes over the outer cover. The stem is part of the fitting that goes into the inner diameter of the inner hose.
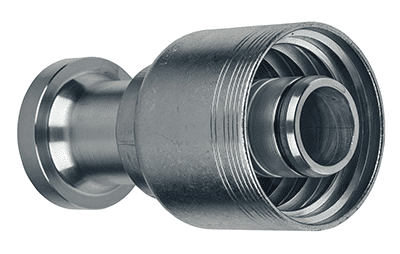
Choosing Appropriate Hose Materials by Application
We see there are some subtle and not-so-subtle differences between hydraulic and industrial hose components. But it doesn’t end there. The material your hose is constructed from can have a major impact on the performance and safety of your assembly.
Commonly used tubing and hose material includes:
- PVC is a low-cost and flexible option that offers chemical and corrosion resistance for use in industrial applications.
- Polyurethane is a popular choice for high-pressure industrial applications and is more resistant to harsh working conditions than PVC.
- Nylon (high-pressure) and polyethylene (low-pressure) are less flexible than PVC and polyurethane but ideal for industrial applications (for example: straight piping around plants and machinery.)
- Polypropylene has strength, flexibility, kink resistance and some chemical resistance with a working pressure of 150 psi for industrial or pneumatic use.
- PTFE (Teflon) or fluoropolymer offers strength, kink resistance and some chemical resistance and can also be used around static electricity but it is not as flexible as other materials.
- Metal core allows the hose to flex and bend without breaking.
- Thermoplastic hose is ideal for hydraulic pressure impulses and can withstand pressure spikes.
- Nitrile rubber is a common hydraulic hose material and may have a textile braid for low-pressure applications or a high-tensile strength steel wire braid for higher pressures.
- Thermoplastic polyurethane is constructed of a nylon tube and synthetic fiber reinforcement and can be used in high-pressure hydraulic applications where wire reinforcements aren’t necessary.
Note from Power & Motion: When choosing hoses, it is mandatory to consult a compatibility chart to check that the tube compound is compatible with the fluid used in the system. Elevated temperature, fluid contamination, and concentration will affect the chemical compatibility of the tube and fluid. Most hydraulic hoses are compatible with petroleum-based oils. Note that new readily biodegradable or green fluids may present a problem for some hoses.
Top Ways to Protect Hoses and Extend their Service Lives
In addition to choosing the proper components that make up your hose assembly, there are additional ways to protect against abrasion, heat, corrosion and other environmental factors. To protect your hose assembly, consider adding the following:
Fire sleeves can protect hoses, cables and wires where high heat, flame and molten metal may be present such as in steel plants, welding shops or other extreme environments.
Spring and spiral guards protect hoses against abrasion and keep hoses free of kinks that may occur as the hose flexes. Spring and spiral guards are available in metal (used in high-pressure or steel-reinforced hoses) or plastic options to protect hoses and wiring from harsh environments.
Protective sleeves and covers protect the inner layers of your hose. Choose protective sleeves and covers that can withstand the conditions of your worksite or plant and meet manufacturer recommendations for pressure, chemical compatibility and other ratings.
Hose protection wrap can detect fluid leaks from failed hoses quickly for rapid repair response, less cleanup and downtime and improved worker safety.
Abrasion Sleeves protect hoses from degradation from friction that occurs over time. Usually made from lightweight urethane, abrasion sleeves allow hoses to move freely and protect against damage resulting from rubbing against themselves and other system components.
For more ideas on extending the service life of your hoses, read How to Protect Hydraulic Hoses for Longer Service Life.
Having Hose Assembly Difficulty?
Even if you have assembled hose lines for years, you can still run across challenges, especially when working with new applications or brands. If a new assembly has you at a loss, it may be a compatibility issue.
As lines evolve or you change suppliers, you may find that hoses and fittings aren’t matching up. That’s why we always recommend using the same brand manufacturer for both hoses and their fittings. Just like hoses, fittings have to meet certain specifications for safe and reliable operation. When you mix and match brands, you run the risk of hose assembly failure.
Related: Premature Hydraulic Hose Failure Costs and Prevention Tips
Superior Industrial Supply knows how important it is to have access to the right hydraulic and industrial hoses and fittings your operations demands. It’s why we specialize in hose assembly and repairs, as well as industrial and MRO supply and fastener selection.
We carry everything you need for your hose assemblies from top-rated brands like Danfoss Power Solutions. Give us a call at 314-638-6500 OPTION 4 or 800-783-6501 and let us know how we can help you find the products, services and advice you need.